With the continuous advancement of modern pharmaceutical technology, the demand for drug packaging has become increasingly diverse, especially for products susceptible to moisture and external environmental factors. Effervescent Tablet Packaging, as an innovative packaging solution, not only effectively preserves the quality and efficacy of medications but also addresses many packaging challenges. Today, we will explore the advantages and applications of Effervescent Tablet Packaging from various perspectives.
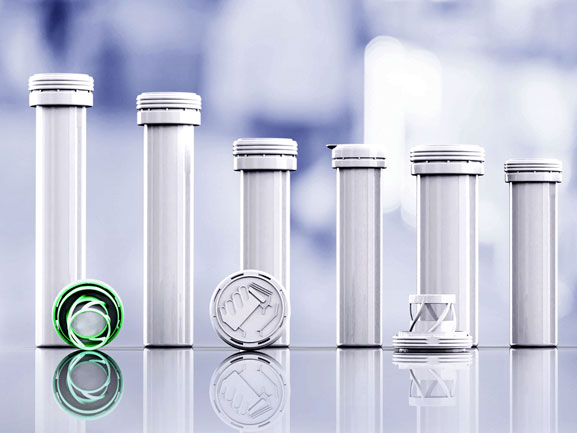
Effervescent tablet packaging
What is Effervescent Tablet Packaging?
Effervescent Tablet Packaging is a specialized moisture-proof packaging designed for small pharmaceutical and health products, typically consisting of a cap and a tube. Its primary function is to protect medications from external factors such as air, moisture, and contaminants, ensuring the integrity and stability of the product. It is particularly suitable for packaging items like vitamin C effervescent tablets, chewable tablets, and similar products.
The design of Effervescent Tablet Packaging emphasizes not only moisture resistance but also convenience, durability, and user experience. Its versatility has led to widespread adoption across multiple industries, particularly in modern pharmaceutical and nutraceutical packaging, where it holds a significant position.
Cap Design: Spring-Loaded vs. Non-Spring-Loaded Caps
The cap of Effervescent Tablet Packaging is a critical component in ensuring drug quality. Depending on the requirements of different medications, there are two main types of cap designs: spring-loaded caps and non-spring-loaded caps.
A spring-loaded cap is a specially designed cap with multiple meticulously constructed components. It includes a desiccant, cardboard, a spiral spring, and a tamper-evident ring to prevent external environmental factors from affecting the medication. The top of the cap features a small compartment for storing the desiccant, preventing direct contact between the desiccant and the medication, which could otherwise cause reactions. The spring, made of soft LDPE material, compresses the tablets to avoid damage caused by external pressure during transportation. The tamper-evident ring allows consumers to visually confirm whether the packaging has been compromised upon first opening. Spring-loaded caps are particularly suitable for larger-dosage medications, such as VC effervescent tablets, which require higher security and protection.
The key difference between non-spring-loaded caps and spring-loaded caps is the absence of a spring mechanism, though they still provide sufficient moisture resistance. These caps are typically used for smaller-dosage medications and supplements, such as vitamin chewables or small candy tablets. Despite their simpler design, non-spring-loaded caps are made from high-quality materials to ensure moisture protection. For some manufacturers of VC effervescent tablets, non-spring-loaded caps remain a popular choice due to their cost-effectiveness while maintaining drug safety.
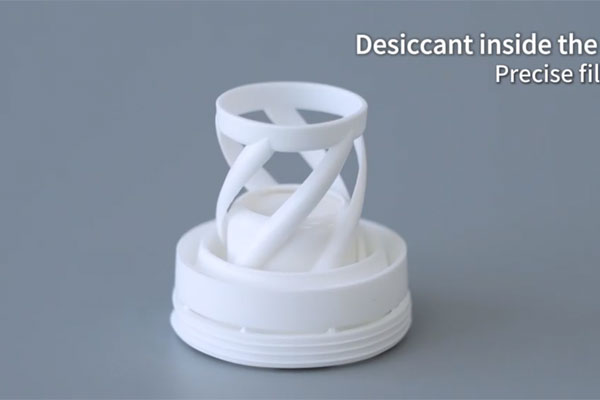
cap for effervescent tube
Advantages of Effervescent Tablet Packaging
Exceptional Moisture Resistance
The standout advantage of Effervescent Tablet Packaging is its superior moisture resistance. Whether in humid environments or during transportation, it effectively isolates external moisture, preventing drugs from deteriorating due to dampness. For moisture-sensitive medications like vitamin C, Effervescent Tablet Packaging provides an ideal solution.
Tamper-Evident Design
The tamper-evident ring in spring-loaded caps is a key highlight. Before the package is opened, the ring remains locked, allowing consumers to clearly identify whether the packaging has been tampered with. This design enhances drug safety and provides additional consumer assurance.
Eco-Friendly and Safe
The materials used in Effervescent Tablet Packaging typically comply with environmental standards, including recyclable plastics, aligning with modern sustainable packaging trends. Moreover, the airtight sealing reduces drug exposure to external air, light, and other harmful factors, effectively extending shelf life.
Portability
Effervescent Tablet Packaging is compact, lightweight, and easy to carry and store. Its design is ideal for daily use, especially for medications like chewables and effervescent tablets that need to be carried frequently. Users can conveniently place the tube in a bag for on-the-go use.
The design and application of Effervescent Tablet Packaging fully reflect the innovation and development in pharmaceutical packaging to ensure drug quality, safety, and convenience. With the continuous emergence of new drugs and formulations, the design and materials of Effervescent Tablet Packaging will continue to evolve to meet more refined market demands.
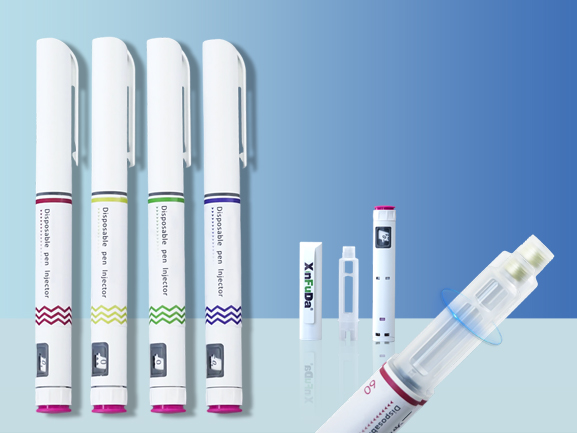
disposable pen injector