Introduction
The Food and Drug Administration (FDA) receives many questions about the labeling of dietary supplements. These questions are a consequence of the activity in this area over the past several years. Some of the important events relating to the labeling of dietary supplements include:
The Nutrition Labeling and Education Act of 1990 amended the Federal Food, Drug, and Cosmetic Act (the act) in a number of important ways. Notably, by requiring that most foods, including dietary supplements, bear nutrition labeling.
The Dietary Supplement Health and Education Act of 1994 (the DSHEA) amended the act, in part, by defining "dietary supplements," adding specific labeling requirements for dietary supplements, and providing for optional labeling statements.
On September 23, 1997 (62 FR 49826), we implemented the DSHEA by publishing several key regulations on the statement of identity, nutrition labeling, ingredient labeling, and nutrient content and health claims for dietary supplements. On June 5, 1998 (63 FR 30615), we amended the regulations pertaining to the nutrition labeling of extracts used in dietary supplements.
On January 15, 1997 (62 FR 2218), we published regulations that require a label warning statement on dietary supplements with added iron. These regulations also required the unit-dose packaging of supplements containing 30 milligrams or more, but this requirement has been eliminated as a result of a court challenge in January, 2003.
On July 11, 2003 (68 FR 41434), we published a final regulation that amended the labeling requirements for dietary supplements, as well as for conventional foods, that would make the declaration of trans fat mandatory in nutrition labeling. This regulation requires that, when present at 0.5 g or more, trans fat be listed in the Supplement Facts panel of dietary supplements on a separate line under the listing of saturated fat by January 1, 2006.
We have prepared this guide to help assure that the dietary supplements sold in the United Stated (U.S.) are properly labeled. This guide applies to dietary supplements produced domestically as well as those produced in foreign countries. Under our regulations, label approval is not required to import or distribute a dietary supplement.
We have included the most frequently raised questions about the labeling of dietary supplements using a "question and answer" format. If you have a question not addressed in this guide, please contact an FDA District Office (see Appendix A of this guide) or the:
Division of Dietary Supplement Programs (HFS-810)
Office of Nutritional Products, Labeling, and Dietary Supplements
Center for Food Safety and Applied Nutrition
Food and Drug Administration
5001 Campus Drive
College Park, MD 20740-3835
240-402-2375
Please be advised that you must comply with any requirements for dietary supplements that may publish after this booklet is issued. New regulations are published in the Federal Register prior to their effective date and are compiled annually in Title 21, Part 101 of the Code of Federal Regulations (21 CFR 101). Summaries of our new regulations (proposed regulations and final regulations) are posted on our Internet Website (http://www.fda.gov).
FDA's guidance documents, including this guidance, do not establish legally enforceable responsibilities. Instead, guidances describe the agency's current thinking on a topic and should be viewed only as recommendations, unless specific regulatory or statutory requirements are cited. The use of the word "should" in agency guidances means that something is suggested or recommended, but not required.
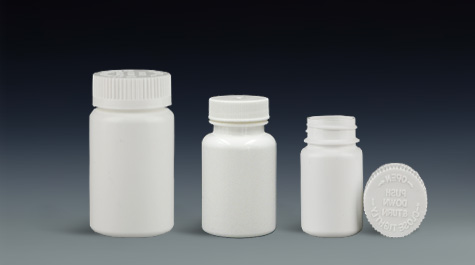
HDPE pills bottle
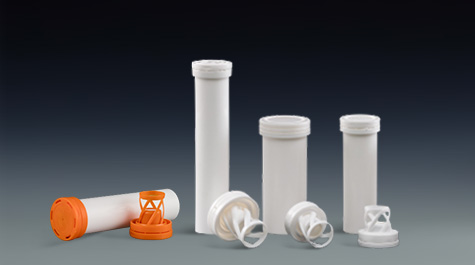
effervescent tablet packaging
Resources come from FDA Web